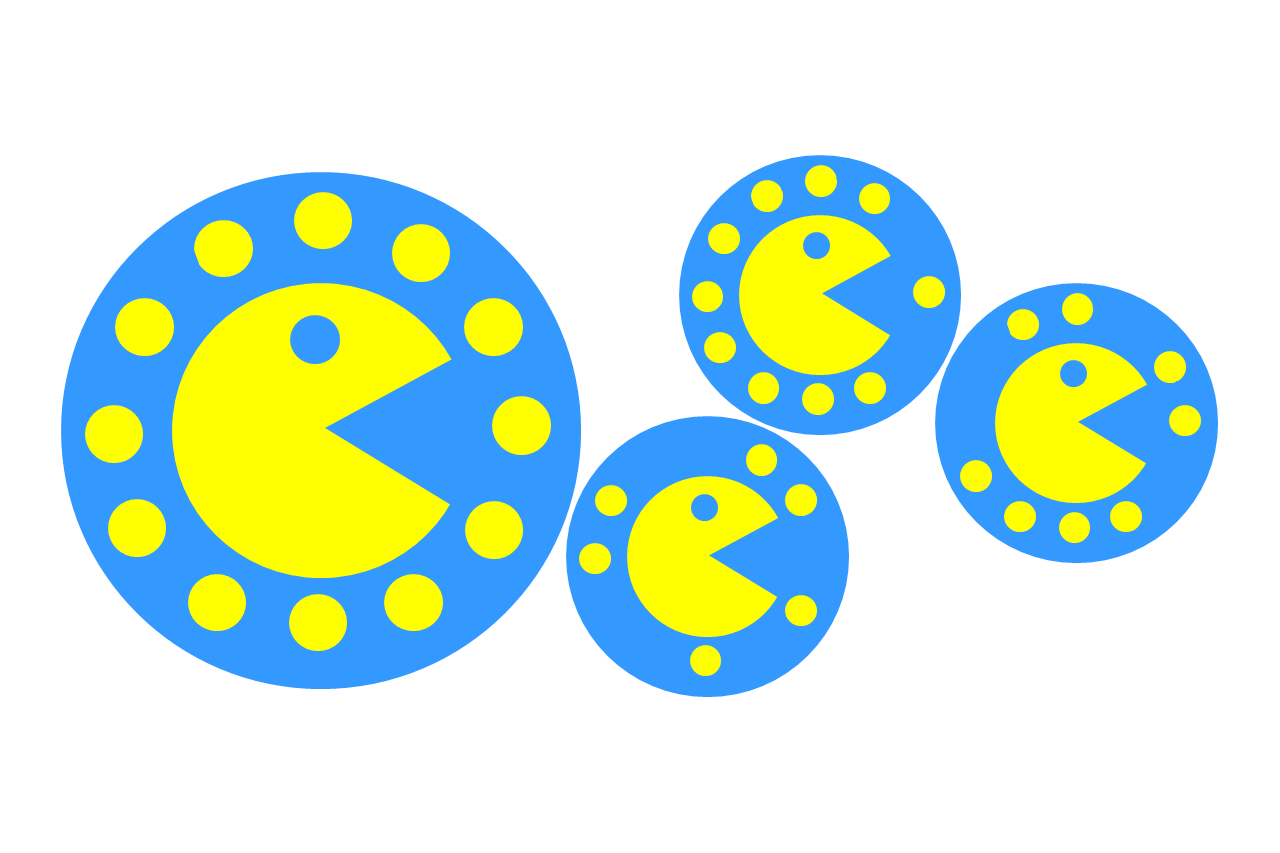
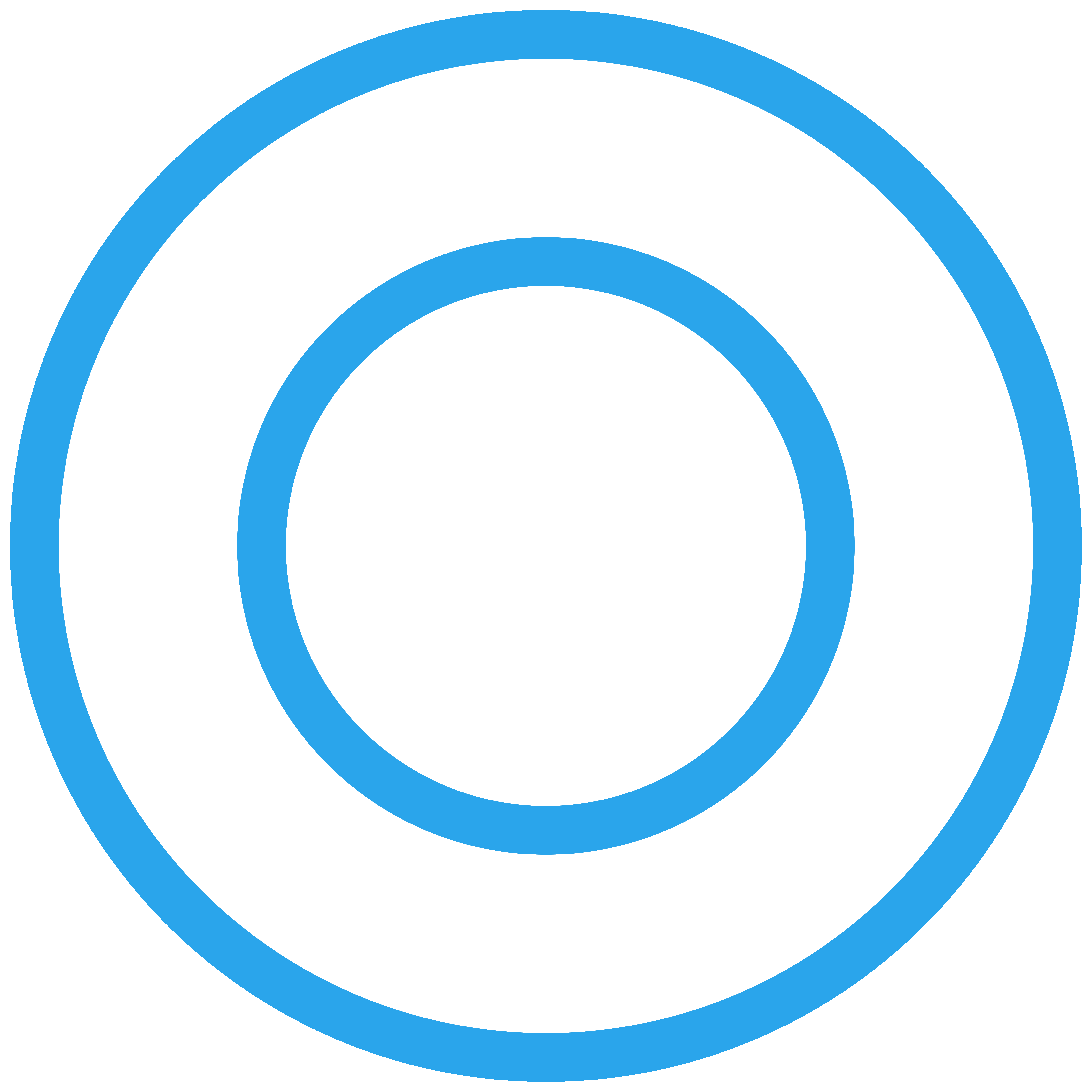
Concentric Sheath/Core
Typically used in binder fibers with a low-melting sheath around a higher-melting core. A nonwoven fabric is made with these fibers, then heated to melt the sheath, which bonds the fabric together upon cooling. The concentric sheath/core can also be used to deliver an outer layer of a high value (and/or low strength) polymer around a lower cost, yet stronger core.
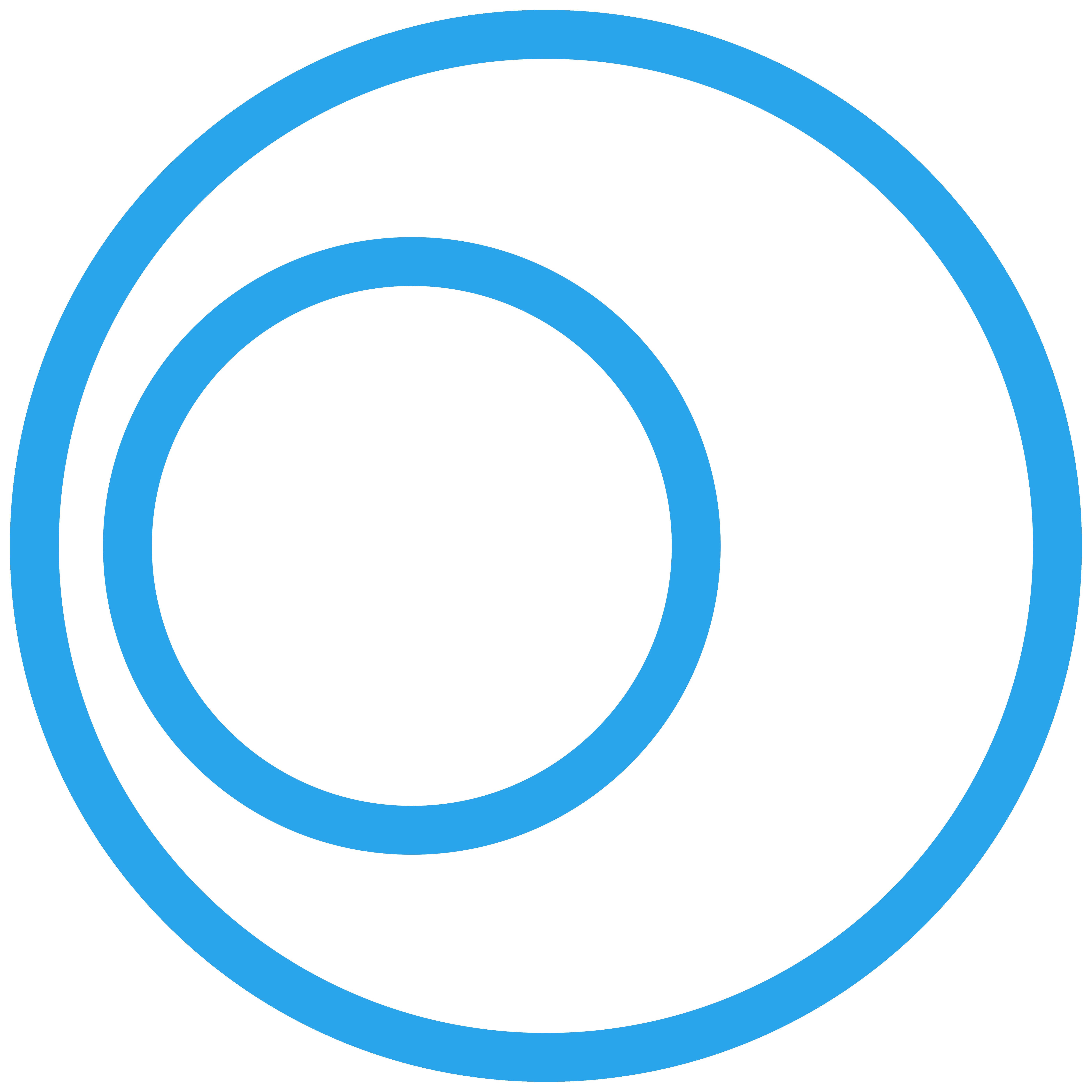
Eccentric Sheath/Core
Similar to the concentric sheath/core, but with the core shifted off-center. The different shrinkage rates of the two polymers causes the fiber to curl into a helix when heated under relaxation. This allows an otherwise flat fiber to develop crimp and bulk.
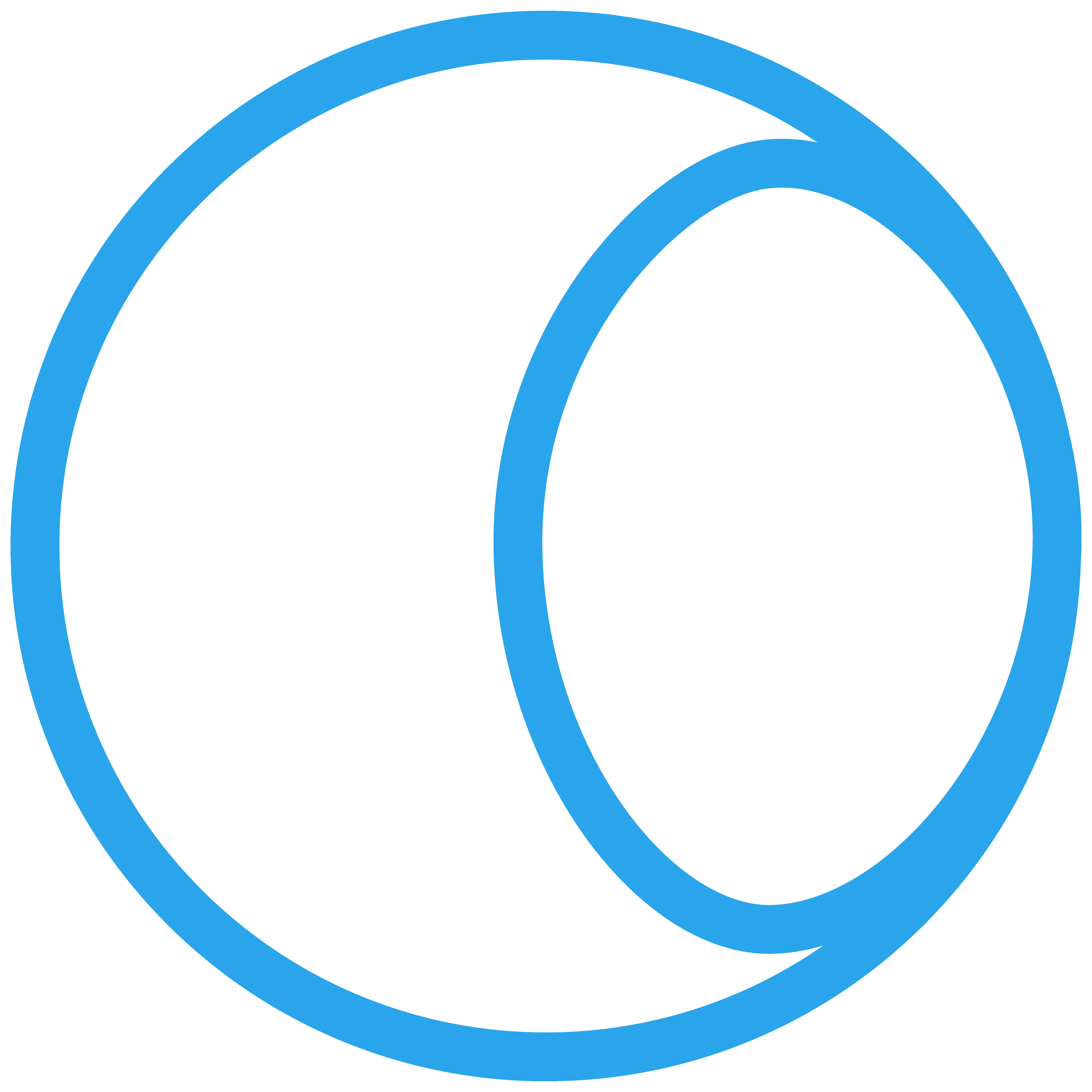
Side-by-Side
A further extension of the eccentric sheath/core fiber, in which both polymers occupy a part of the fiber surface. With proper polymer selection, this fiber can develop higher levels of latent crimp than the eccentric sheath/core.
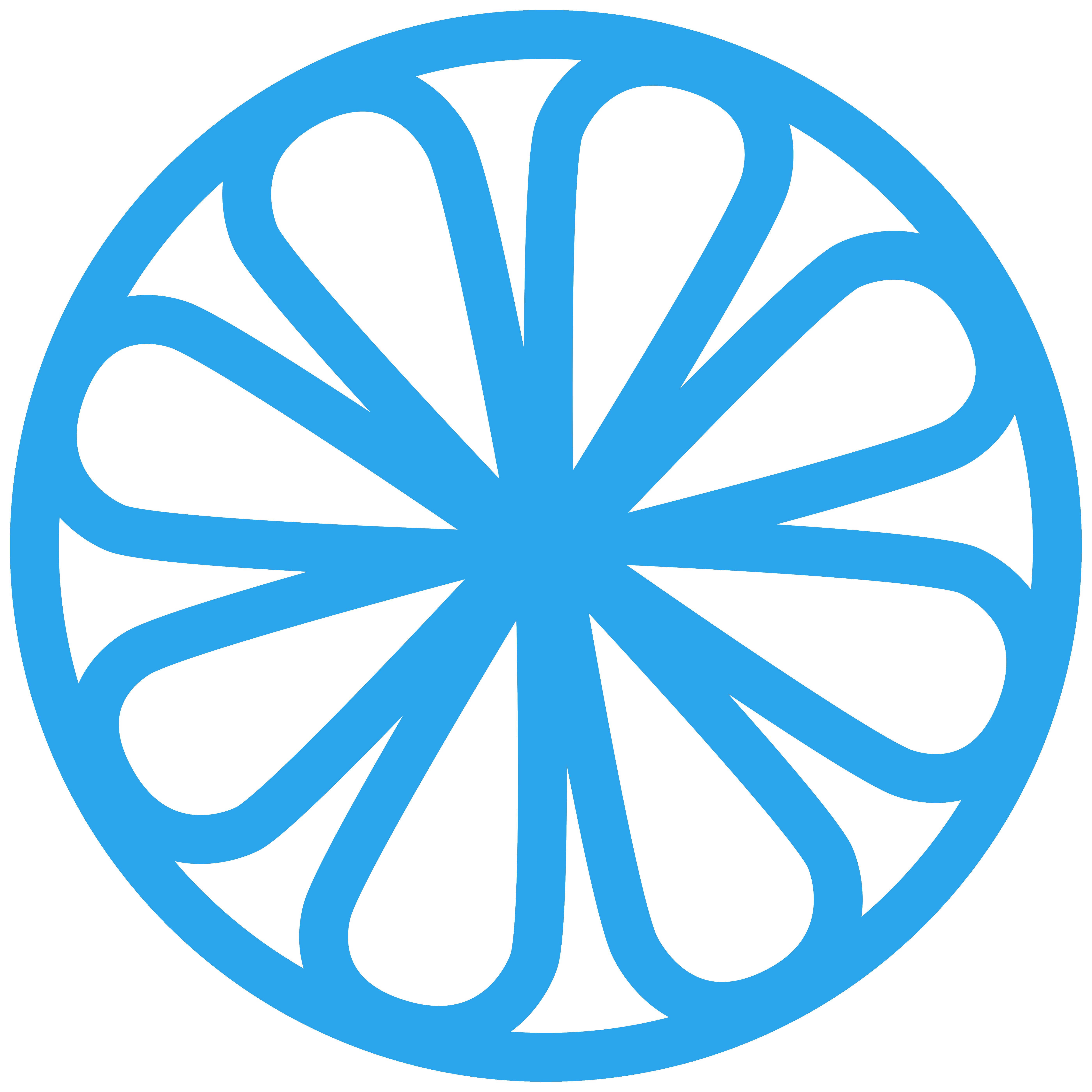
Pie Wedge
A round cross section made of 16 adjacent wedges, similar to slices of pie. Each wedge of polymer A has a wedge of polymer B on either side, for a total of 8 wedges of each polymer. These fibers are designed to be split into the component wedges by mechanical agitation (typically hydroentangling), yielding microfibers of 0.1 to 0.2 denier in the final fabric. You can download our paper describing novel uses for splittable fibers.
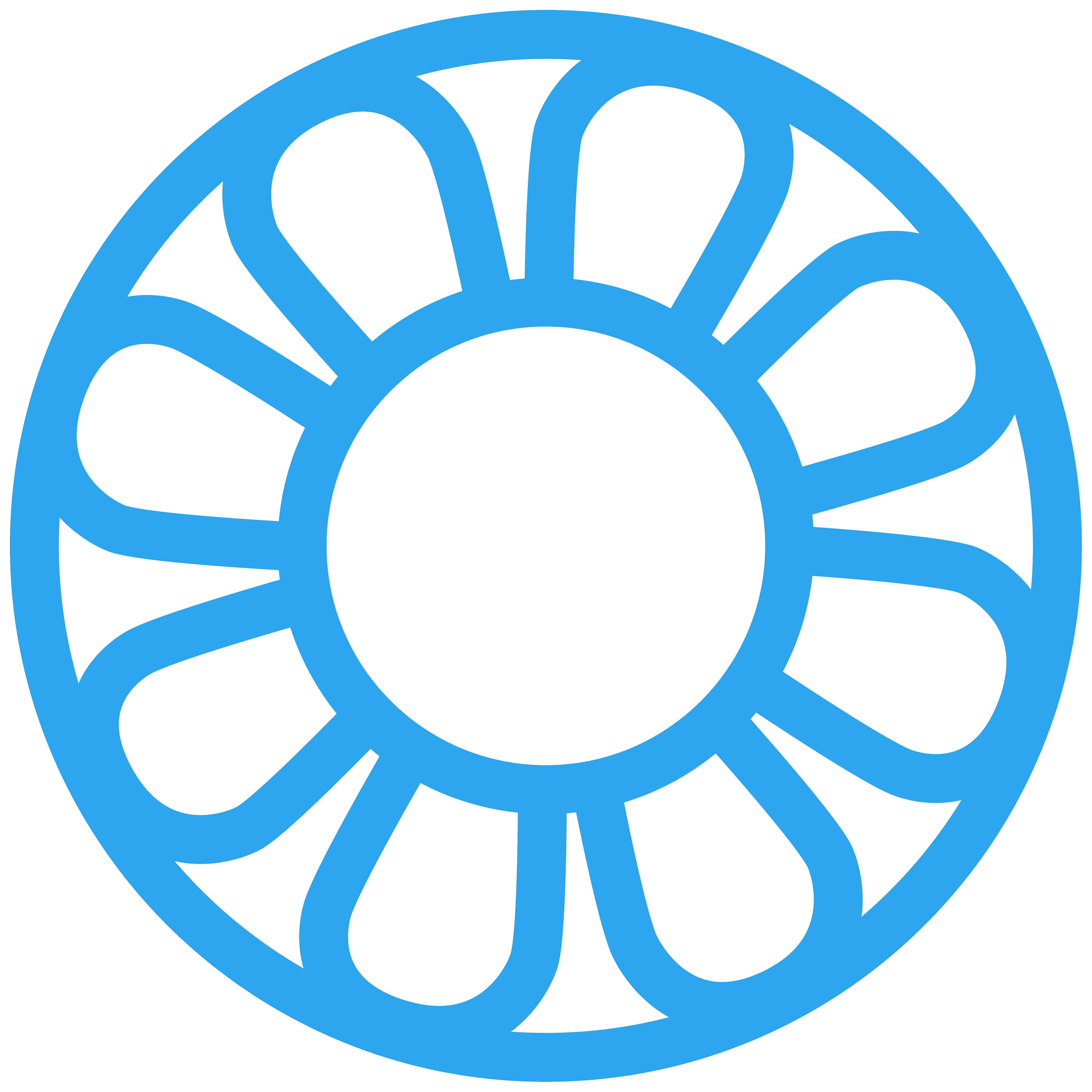
Hollow Pie Wedge
Similar to the above but with a hollow center core that prevents the inner tips of the wedges from joining; thus making splitting easier. Hollow centers can be used in other fibers, too, but are particularly useful here. Novel applications for these fibers are also discussed in our paper on splittable fibers.
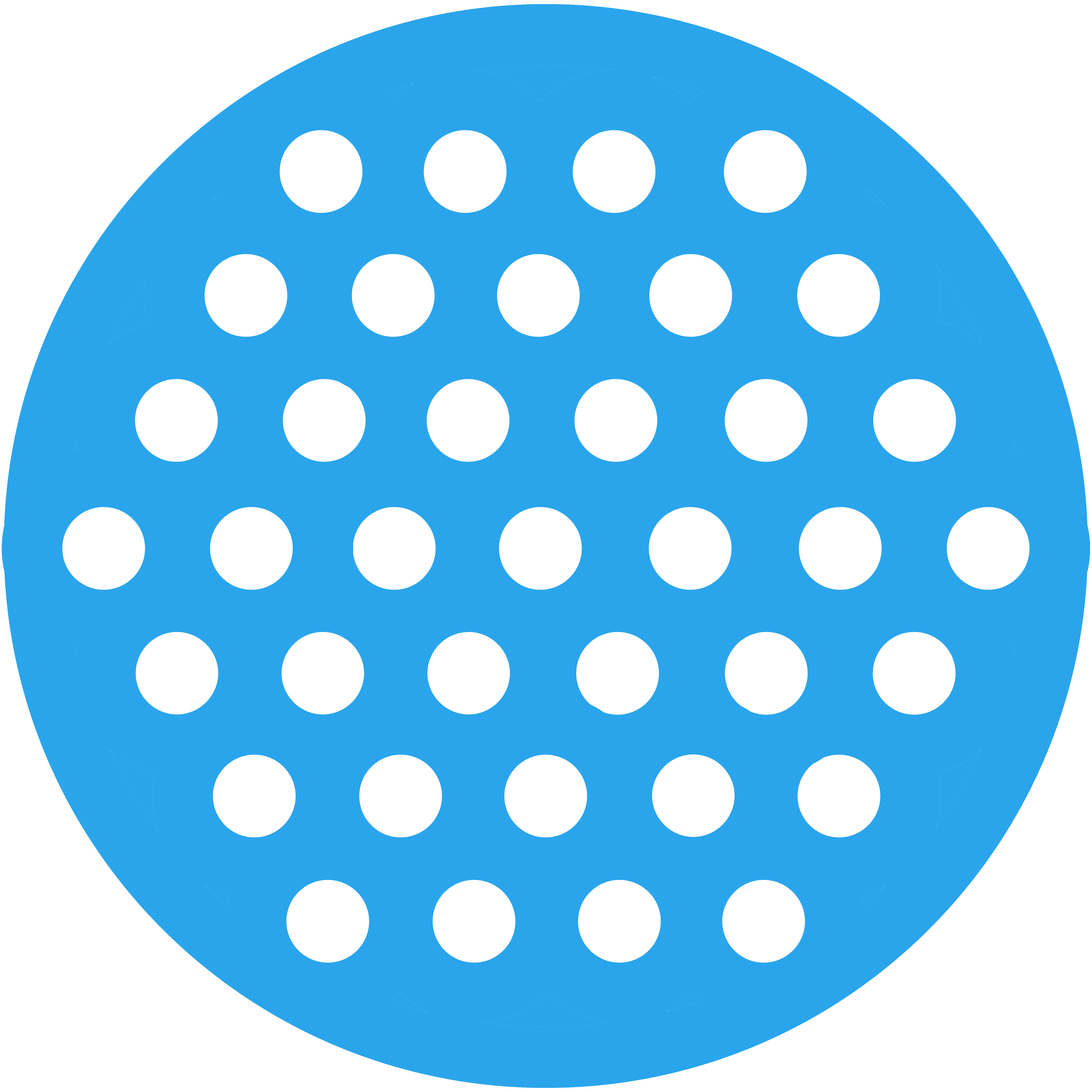
Islands/Sea
Also known as the "pepperoni pizza" configuration where polymer A is the pepperoni and polymer B is the cheese. This fiber allows the placement of many fine strands of a fiber polymer within a matrix of soluble polymer that is subsequently dissolved away. This allows the production of a fabric made of very fine microfibers because the fibers are easier to process in the "pizza" form rather than as individual "pepperonis." Staple fibers can be made with 37 pepperonis on each pizza, producing fibers as low as 0.04 denier (about 2 microns diameter). We are working on methods to make these fibers even smaller.
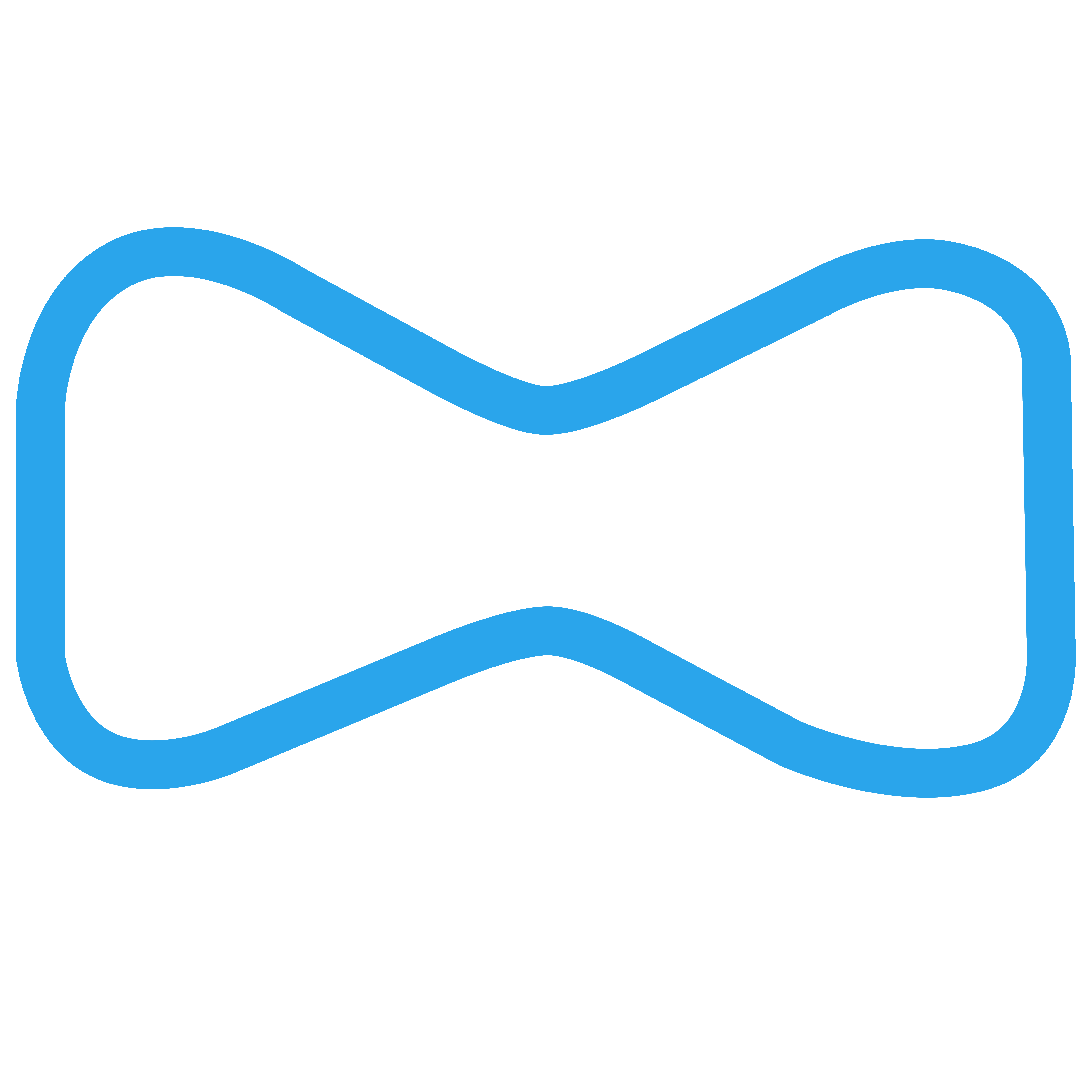
Bowtie
The bowtie cross section was developed for a side-by-side bicomponent filament yarn that provides gentle stretch recovery. The cross section optimizes the separation of the centers of mass of the two respective polymers, thus enhancing the stretch recovery of the helically-coiled fibers.
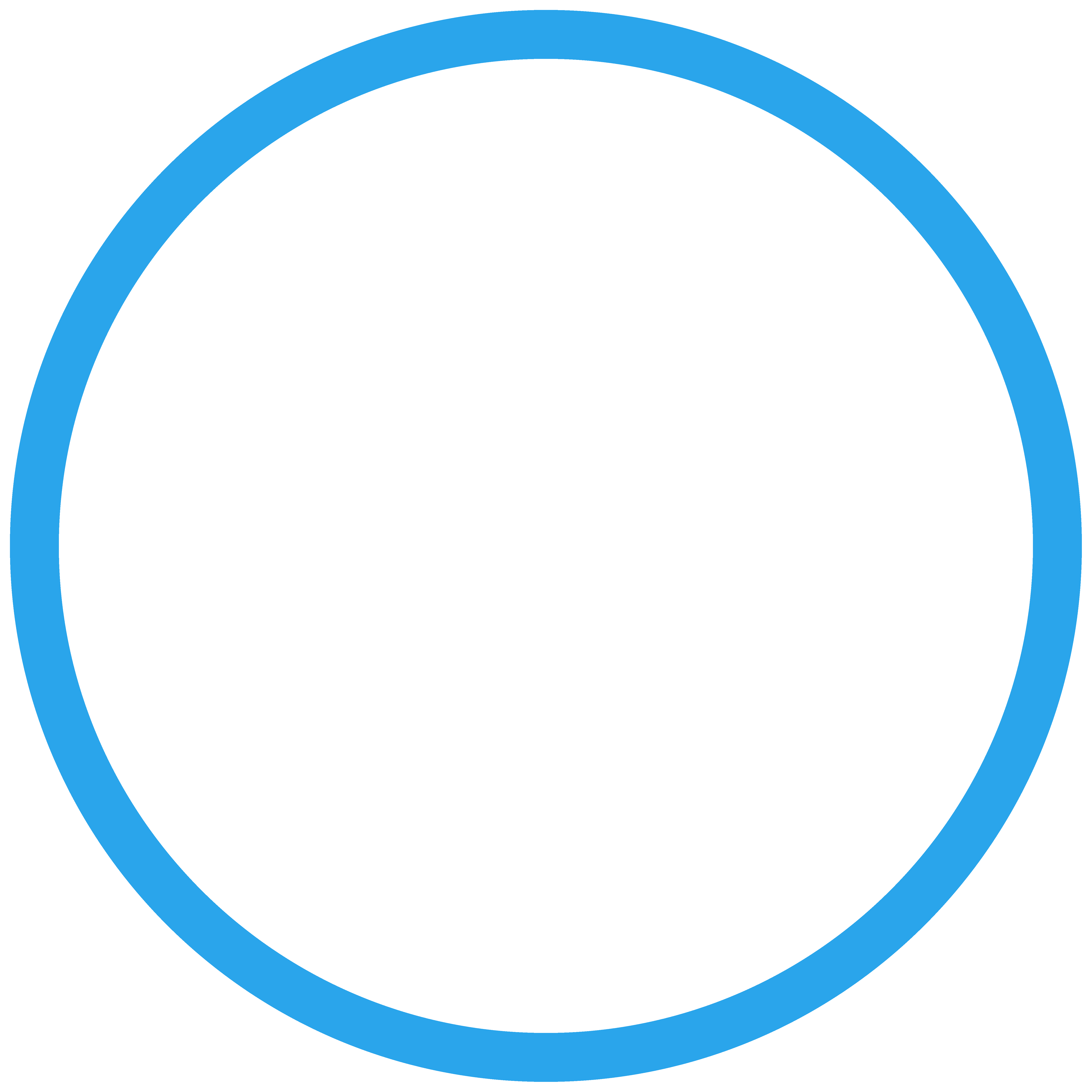
Solid Round
This is the standard cross section for most synthetic fibers. It has a minimum surface to volume ratio, but in most cases it is used simply because it is usually less expensive than modified cross sections.
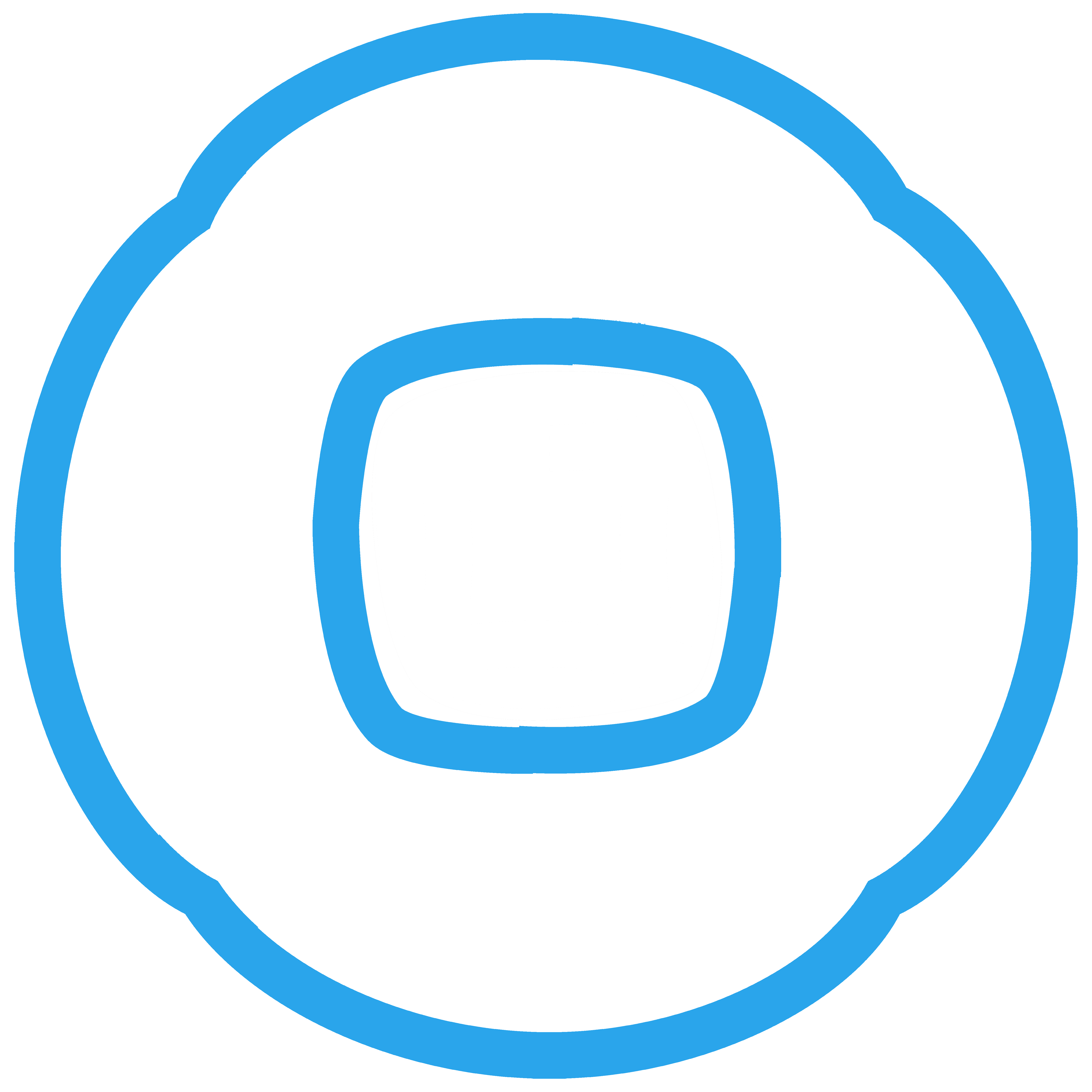
Hollow
The hollow cross section has at least one hollow void enclosed within the fiber and running the entire length of the fiber. Hollow fibers are usually round, but need not be. They feature:
- higher specific surface areas
- lower density at the same diameter
- thermal insulation properties due to trapped air
- higher specific rigidity, so long as the hollow void does not collapse
- a delustered (less shiny) appearance.
Hollow fibers are generally NOT useful for wicking of aqueous fluids.
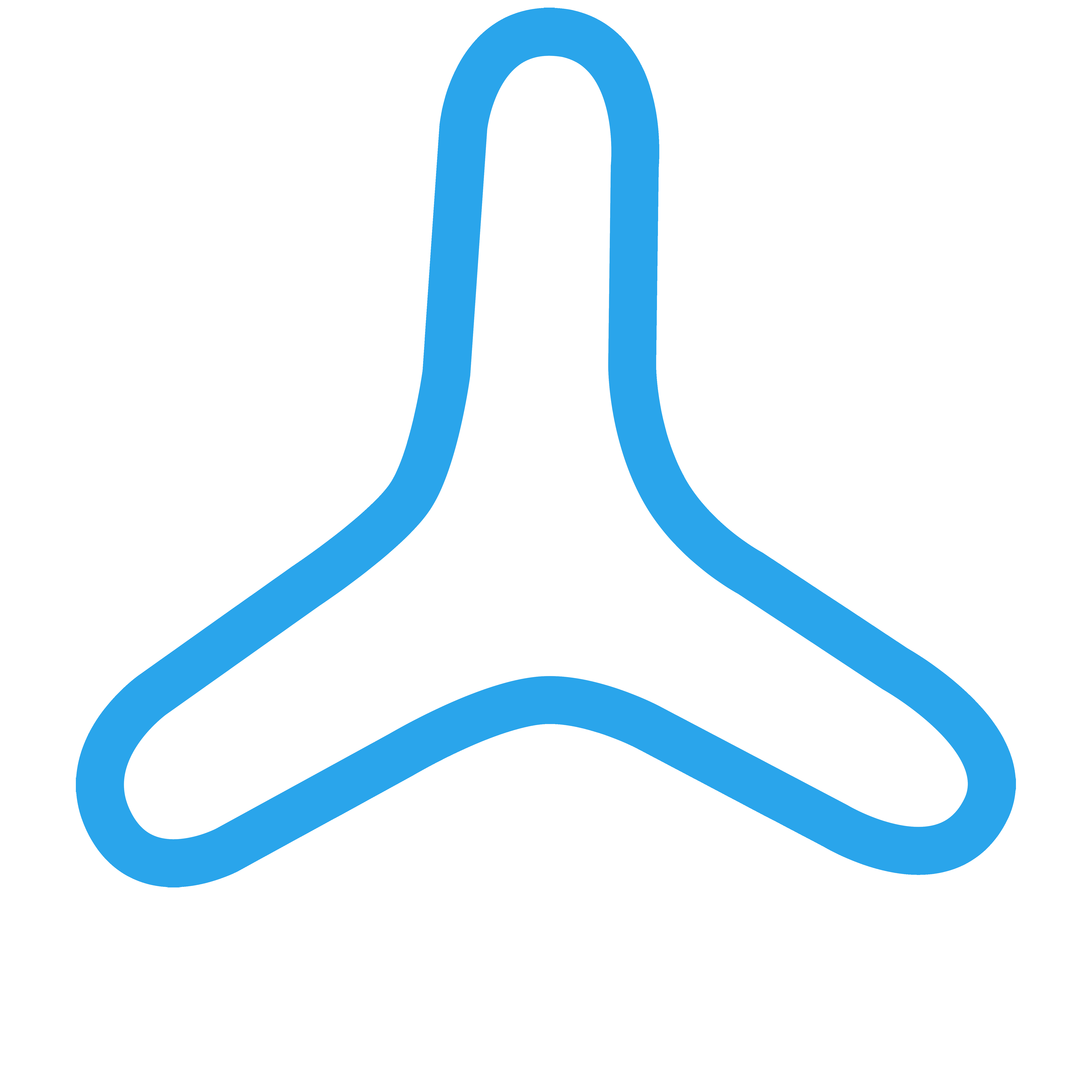
Trilobal
A trilobal fiber gives a fiber rigidity and resilience, and the many reflecting surfaces are efficient at scattering light to hide dirt. For these reasons, trilobal fibers are often used in carpets. The reflective surfaces can also give the fiber a sparkling appearance.
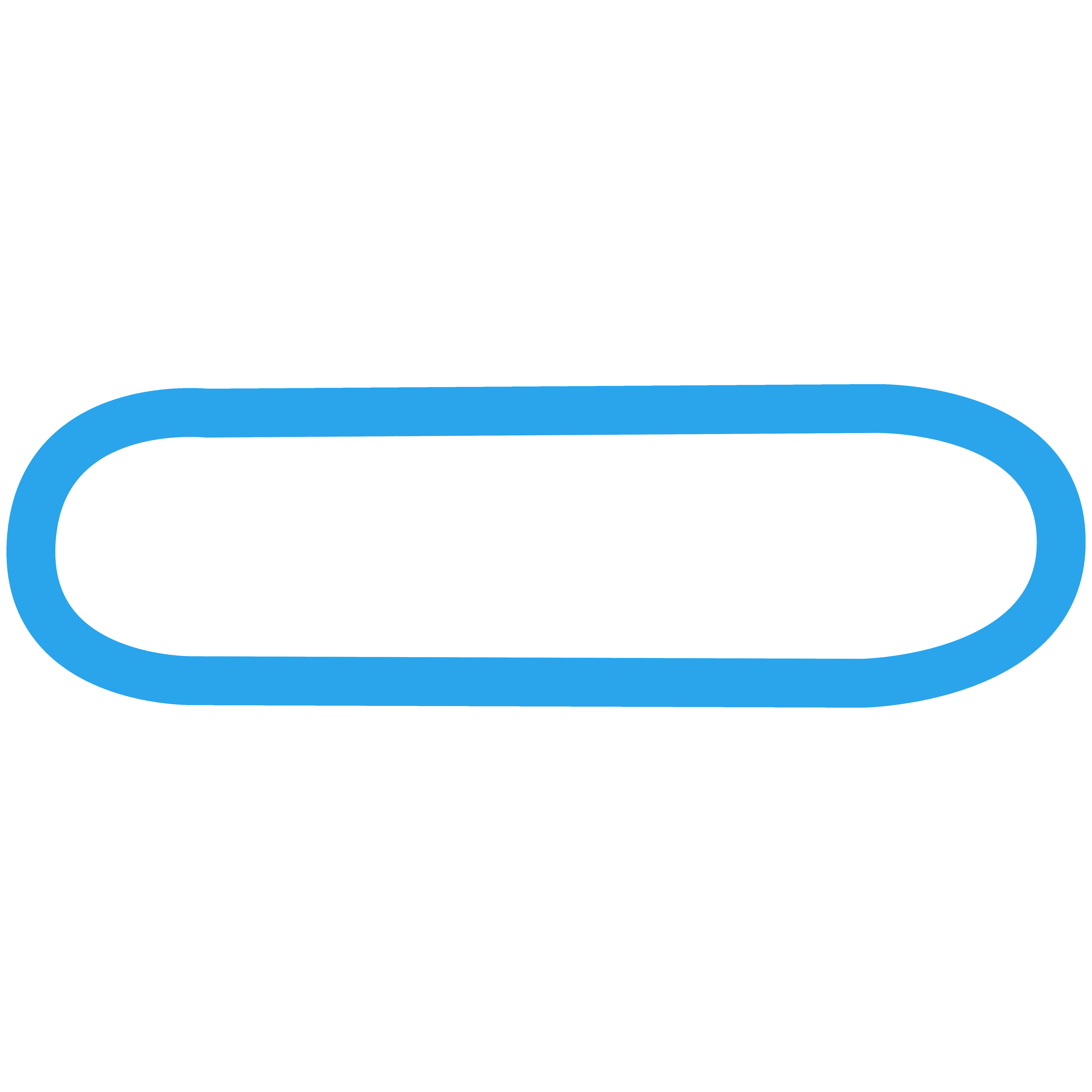
Ribbon
A ribbon cross section provides large flat surfaces for specular reflection of light, so its appearance is highly sparkling. It also has a preferred bending direction, which makes it difficult to card. If a segmented bicomponent cross section (like a pie wedge) is made with a ribbon cross section, it is exceptionally easy to split into microfibers.
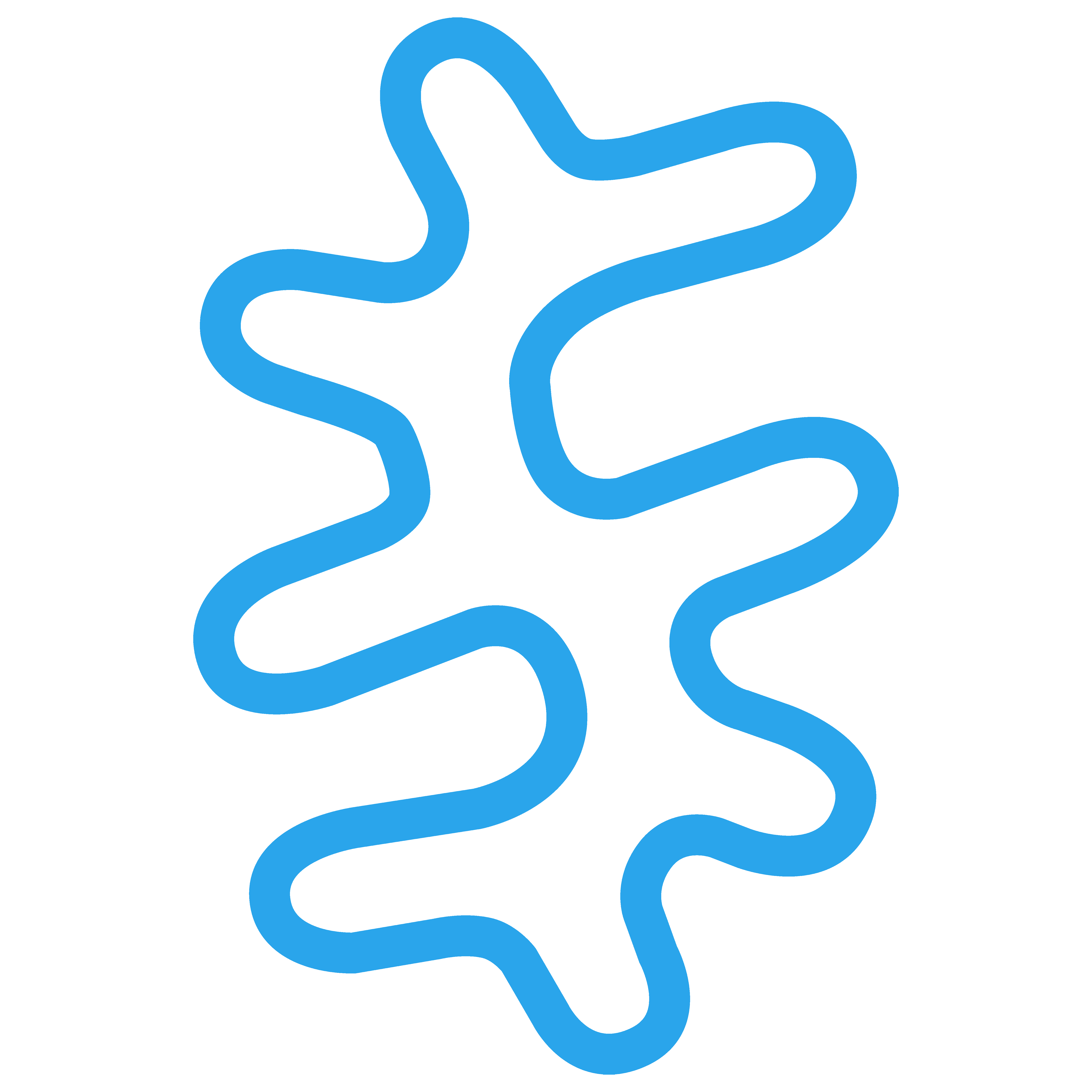
4DG™
This highly modified cross section was created for moisture transport, using capillary wicking in its many grooves. It is the most effective moisture transport fiber commercially available. Its high surface area and deep grooves also make it highly effective in thermal insulation, filtration, and in delivering materials from its grooves.